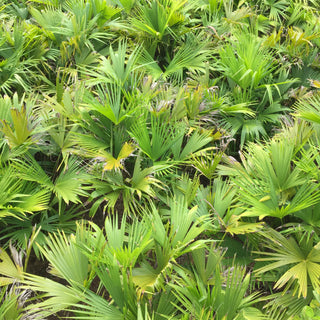
THE JIPIJAPA PLANT: MAGIC THAT EMERGES FROM PLANTS AND YUCATECAN TALENT
Maybe you have seen it in a garden, in a park or on a road; It may even be that it is already in your closet, since the jipijapa plant is used to make different pieces of clothing such as hats, earrings and more.
The jipijapa, also called toquilla or panama plant (the latter in honor of the bridge on which hats made with this material were exported), comes from the lowlands in Ecuador and owes its name to the small town of the same name in the Province of Manabí. Although the plant is not endemic to Yucatán, it became popular since the 1800s, when the brothers Sixto and Pedro García introduced the plant to Mexico by planting jipijapas on the henequen hacienda of Santa Cruz, in Calkiní, after a trip through Guatemala.
Nowadays, as the years go by, this plant is found everywhere in Yucatán and Campeche, and accessories made from it are successfully marketed in the state due to its fresh & light appearance, quality and its natural origin, in addition of the sustainable process that goes into producing one.
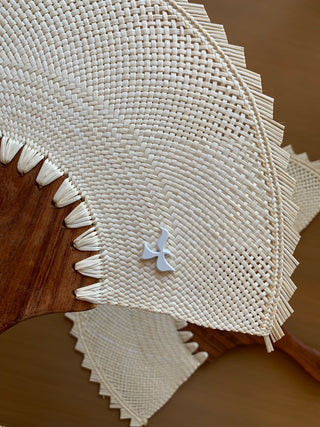
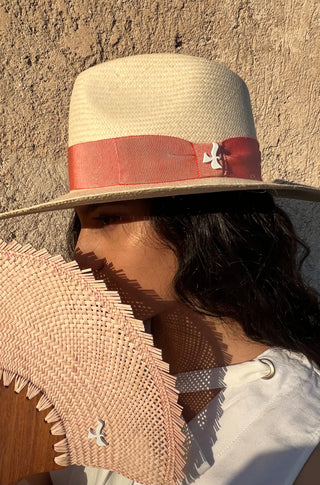
.
Now, it is a fact that this material is beautiful and unique, but how does a beautiful plant in a field transform into something as wonderful as a hat or fan? We took on the task of finding out from Don Carmito (José), one of the artisans in the Jipijapa group in Campeche, what the manufacturing process is for a hat, and after a long talk with him, we managed to divide this process into 7 stages:
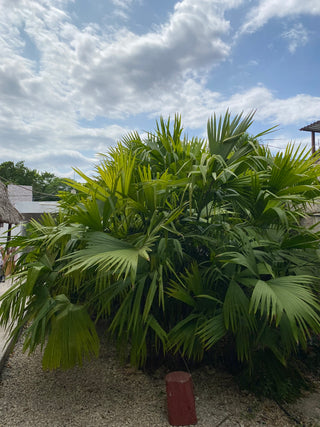
1 & 2
1. The magic begins in a field, when the artisans plant the jipijapa so that it grows, where they take care of it and watch over it. 2. Three years later, the closed leaves are cut (since the open ones are useless
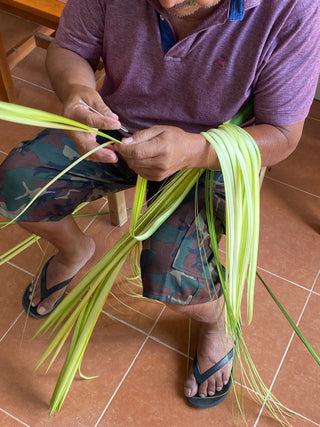
3
The cut leaves are separated depending on quality, which range from 1 to 5 (1 being standard and 5 being the finest). If it is quality 1, the sheets will be separated once, if it is quality 2, they will be separated twice, and so on until quality 5 is reached.
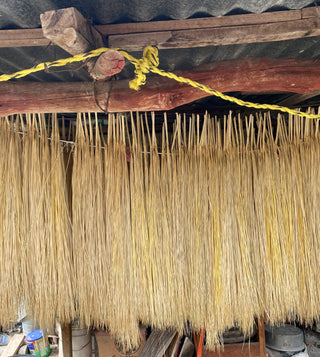
4
The leaves will dry for approximately 8 days. During this process, the branches are laid out, washed with a lot of water and detergent, allowed to drain, and then placed in an "oven" with charcoal and sulfur. This entire process is repeated twice. It is important that the leaves dry after baking to avoid the appearance of mold, as well as being careful with the sun to avoid color change.
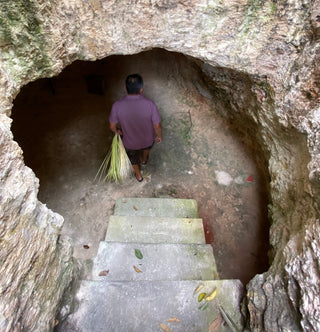
5
When the branches are ready to weave, they are placed in a cave overnight, as they need moisture, which serves to keep them flexible and easy to weave. The caves in which hats are woven can be natural or artificial. Natural refers to the fact that they have found a cave in the space in which they work, and artificial is one made with their own hands digging. It takes at least 4 months to build a cave in the ground, which are not that deep due to the nature of the land in Yucatan.
6. To maintain the shape of the hat while it is woven, artisans use molds made from local wood, such as guayacán, sapodilla, tzalam or Caribbean walnut. In this way, the hats begin to be knitted. The production time depends on the quality of the hat, for example, for a standard quality (quality 1) about 20 hours of knitting are required, while for the finest quality it takes up to a month.
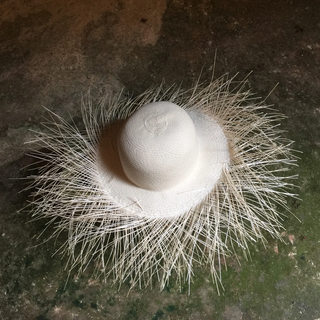

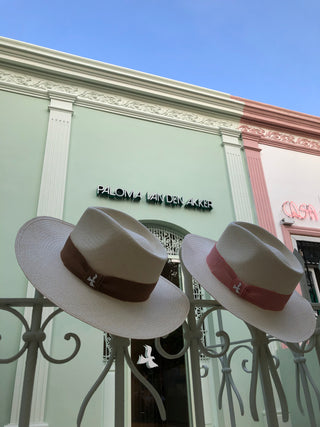
7
Finally, the hat is ironed on a special press to shape it according to the model. It can be Cuban, American or another mold that they use.This is how, in the end, you achieve a beautiful, unique, fresh and special hat.
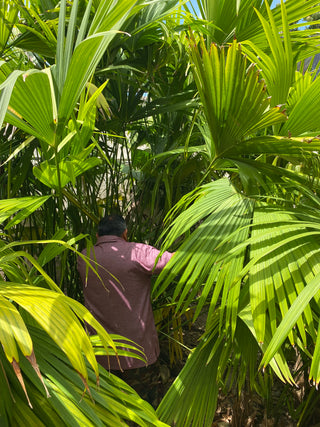
The knowledge of the artisans was nothing more than transmitted from generation to generation by their parents and grandparents. Currently, it is only adults who dedicate themselves to this craft, as young people prefer to take another path due to the laborious process involved in making them and the social point of view that working in crafts currently has, in addition, in some cases, the Payment for these beautiful pieces is not profitable to lead a decent life. This is when we ask ourselves: Will this be the last generation of jipijapa artisans? In us there is the possibility of helping to prevent these techniques from disappearing, giving them the value and recognition they deserve, improving and innovating the conditions and spaces in which artisans work and giving new meaning to the production of crafts, in addition to becoming aware of our decisions, shopping and lifestyle.
Despite everything, in the Mayab interior, there are still artisans willing to delight our eyes with the power of their hands and their talent perfected over the years, made with a lot of love and hope for a better future.
So, we invite you to take a look at these works of art, delight in the texture and workmanship they have; Choose the one that makes you look and feel best, be it Cuban or American, black or pink, and proudly carry the power of the Yucatecan hand. At Paloma van den Akker we will help you choose the best one for you.
Your perfect hat awaits you!
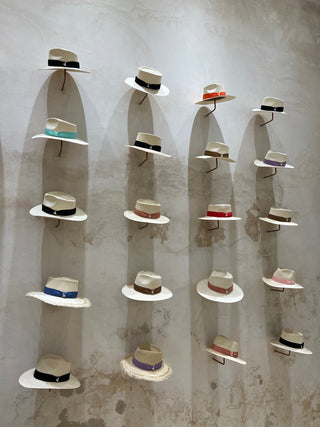
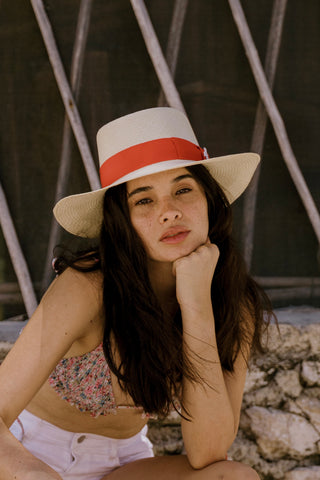